Testing Thermal Performance with the Testo 883 Thermal Imager
By Alex Jaison, Dynamics & Drivetrain 2024
Team Swinburne, the student lead motorsport team just competed in the 2024 race down at Calder Raceway in December, featuring its latest Formula SAE racing car design the TS_24.
Throughout the year, the Team is encouraged and driven to research, design and build the most optimal racing car design, applying classroom knowledge in a real-world application and offering team members with practical skills that can be best learnt in being involved and doing.
This year I found myself investigating the motor controller cold plate and I was tasked to ensure this component would optimise temperatures in the engine during operation, reducing the risk of overheating and ensuring most practical use of physics in the engine’s natural surrounds.
TS_24’s design was crammed full of optimisations and iterative design improvements, one major improvement being the motor controller repackaging. The motor controller is an essential, sensitive component containing four inverters which need to be kept under 40˚C. This is especially challenging during the hot summer afternoons at Calder Park Raceway, where our competition was held mid-December. To achieve this, we use a heat sink in the form of a water-cooled aluminium plate. This year, other improvements to the cooling system invited a redesign of this part.
A huge part of this engineering process is the months of CFD (Computational Fluid Dynamics) made possible by Ansys. Maximal heat transfer is a priority, and the heat generated from the inverters must be dissipated by the flowing water as efficiently as possible. Hence, throughout the CFD process, fluid and cold plate temperatures were tracked to reach an optimal balance. Yet, to verify these computer- generated results, real world tests must be completed on the final product. These tests must be measured accurately and reliably, be replicative of CFD conditions, and also provide a good picture of the expected performance at competition. Luckily, Testo’s infrared camera makes it quick and easy.
To test the effectiveness of the redesigned cold plates, we replicated the thermal load of the inverters with resistors to see how efficiently heat was dissipated. Testo’s thermal camera (testo 883) gave us an intuitive and instantaneous understanding of the cold plate’s reactions to changes in thermal load, coolant temperature, flow rate and more, its high-resolution screen capturing minute details in infrared. We were also able to compare these real-world readings with our CFD results, where the 883’s pinpoint precision was not only beneficial but necessary.
The device is also incredibly user friendly, a feature that makes it perfectly suited to the timeline constraints of Formula SAE and Team Swinburne.
Team Swinburne were able to achieve 3rd in Acceleration, however we suffered some major technical issues and were unable to run in the other dynamic events. Nonetheless, the TS_24 racing car design project taught us a lot of key lessons we will take into 2025.
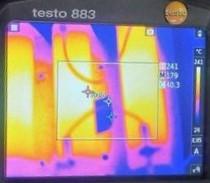
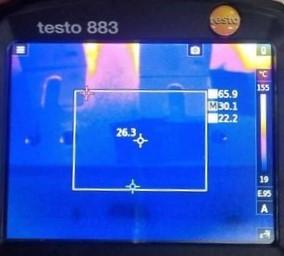